Wankel Engine
The Wankel radial engine is a fascinating beast that features a very clever rearrangement of the four elements of the Otto cycle.
Felix Wankel was born in 1903 in Lahr in the Schwarzwald in Germany. He was employed in the sales department of a scientific publishing house in Heidelburg from 1921 to 1926. In 1924, he set up a workshop in Heidelburg where he made his first models of a rotary piston engine. Realizing that the principal problem with such designs was gas tightness, he spent considerable time attempting to resolve it. By 1927, the problems were largely solved. During World War II, he worked for the German Luftfahrtministerium (Air Ministry). In 1951, Wankel and NSU signed a contract establishing a partnership to develop the rotary piston engine.
On 13 April 1954, the first Wankel rotary engine was built by NSU (DKM 54, Drehkolbenmotor), picture left. In 1956, an NSU prototype motorcycle won all the trials in its category and broke several world records on the Great Salt Lake in the USA - its engine was fed by a Wankel supercharger.
The so-called KKM 57 (the Wankel rotary engine, Kreiskolbenmotor)picture below, was constructed by NSU engineer Hanns Dieter Paschke in 1957 without the knowledge of Felix Wankel, who remarked "you've turned my race horse into a plow mare".
In 1958, NSU started tests on the Wankel engine. In 1960 the Wankel engine was first discussed in public at the congress of the German Engineers’ Association. In 1963, NSU launched the Wankel powered Spider at the Frankfurt Motor Show.
When we have a look at a lifting cylinder engine, we can notice that many parts don't run evenly. They get strongly accelerated and braked again in short time (e.g. piston, connecting rod, valves, valve rods, etc.). This problem was tried to be resolved for a long time by trying to develop something else. Not to use alternating Otto engine, but a turning one. Like that the enormous acceleration forces in the lifting cylinder engine could be avoided, which set a boundary to the numbers of revolutions of the crankshaft.
Already around 1636, a German called Pappenheim sketched a rotary pump, which was used about 150 years later in Watt's steam engines for the first time in practice.
Unfortunately the basic difficulties could not be solved at this time: The sections could not be sealed properly and that's why the efficiency of these rotary engines/pumps was by far worse than in lifting piston engines. Many engineers tried in vain to solve these problems and it didn't seem possible that once an efficient rotary engine will be developed.
The Wankel engine was developed in the 70's by many companies, e.g. by General Motors, Daimler Benz, Peugeot and Mazda. They built altogether over one million wankel engine-operated cars.
But because of the arising environmental regulations and in the consequence of the oil crisis no more investments were done.
Only Mazda continued development with rotary engine. Mazda has been a pioneer in developing production cars that use rotary engines. The RX-7, which went on sale in 1978, was probably the most successful rotary-engine-powered car. But it was preceded by a series of rotary-engine cars, motorcycles, trucks and even buses, starting with the 1967 Cosmo Sport. The last year the RX-7 was sold in the United States was 1995, but the rotary engine is set to make a comeback in the near future.
The Mazda RX-8 , a new car from Mazda, has a new, award winning rotary engine called the RENESIS. Named International Engine of the Year 2003, this naturally aspirated two-rotor engine will produce about 250 horsepower. The Renesis engine – also 13B-MSPv (Multi Side Port) – which first appeared in production in the 2004 Mazda RX-8, is an evolution of the previous 13B. It was designed to reduce exhaust emission and improve fuel economy, which were two of the most recurrent drawbacks of rotary engines. Unlike its predecessors from the 13B range, it is naturally aspirated, leading to lower power.
The engine entailed two major changes. First, the exhausts ports are no longer peripheral but are located on the side of the housing, which allowed engineers to eliminate overlap and redesign the intake port area. This produced noticeably more power, thanks to a better compression ratio. Second, the rotors are shaped differently, especially their side seals and low-height apex seals, which offer optimized lubrication.
These and other innovative technologies allow the Renesis to achieve 49% higher output and dramatically reduced fuel consumption and emissions (the RX-8 meets LEV-II).
In a piston engine, that pressure is contained in the cylinders and forces pistons to move back and forth. The connecting rods and crankshaft convert the reciprocating motion of the pistons into rotational motion that can be used to power a car.
Rotary engines use the four-stroke combustion cycle, which is the same cycle that four-stroke piston engines use. But in a rotary engine, this is accomplished in a completely different way.
The heart of a rotary engine is the rotor. This is roughly the equivalent of the pistons in a piston engine. The rotor is mounted on a large circular lobe on the output shaft. This lobe is offset from the centerline of the shaft and acts like the crank handle on a winch, giving the rotor the leverage it needs to turn the output shaft. As the rotor orbits inside the housing, it pushes the lobe around in tight circles, turning three times for every one revolution of the rotor.
If you watch carefully, you'll see the offset lobe on the output shaft spinning three times for every complete revolution of the rotor.
The best way to visualize the action of the engine in the animation at left is to look not at the rotor itself, but the cavity created between it and the housing. The Wankel engine is actually a variable-volume progressing-cavity system. Thus there are 3 cavities per housing, all repeating the same cycle. Note as well that points on the rotor and e-shaft turn at different speed, e-shaft moves 3 times faster than rotor, so that one full orbit of the rotor equates to 3 turns of the e-shaft. As the rotor moves through the housing, the three chambers created by the rotor change size. This size change produces a pumping action. Let's go through each of the four strokes of the engine looking at one face of the rotor.
Intake
The intake phase of the cycle starts when the tip (apex) of the rotor passes the intake port. At the moment when the intake port is exposed to the chamber, the volume of that chamber is close to its minimum. As the rotor moves past the intake port, the volume of the chamber expands, drawing air/fuel mixture into the chamber. When the peak of the rotor passes the intake port, that chamber is sealed off and compression begins.
Compression
As the rotor continues its motion around the housing, the volume of the chamber gets smaller and the air/fuel mixture gets compressed. By the time the face of the rotor has made it around to the spark plugs, the volume of the chamber is again close to its minimum. Mixture ignites. This is when combustion starts.
Combustion
Most modern rotary engines have two spark plugs. The combustion chamber is long, so the flame would spread too slowly if there were only one plug. When the spark plugs ignite the air/fuel mixture, pressure quickly builds, forcing the rotor to move further in the direction that makes the chamber grow in volume. The combustion gases continue to expand, moving the rotor and creating power, until the peak of the rotor passes the exhaust port.
Exhaust
Once the apex of the rotor passes the exhaust port, the high-pressure combustion gases are free to flow out the exhaust. As the rotor continues to move, the chamber starts to contract, forcing the remaining exhaust out of the port. By the time the volume of the chamber is nearing its minimum, the peak of the rotor passes the intake port and the whole cycle starts again.
The neat thing about the rotary engine is that each of the three faces of the rotor is always working on one part of the cycle. In one complete revolution of the rotor, there will be three combustion strokes.
A rotary engine has an ignition system and a fuel-delivery system that are similar to the ones on piston engines. If you've never seen the inside of a rotary engine, be prepared for a surprise, because you won't recognize much.
Rotor
The rotor has three convex faces, each of which acts like a piston. Each face of the rotor has a pocket in it, which increases the displacement of the engine, allowing more space for air/fuel mixture.
At the apex of each face is a metal blade that forms a seal to the outside of the combustion chamber. There are also metal rings on each side of the rotor that seal to the sides of the combustion chamber.
The rotor has a set of internal gear teeth cut into the center of one side. These teeth mate with a gear that is fixed to the housing. This gear mating determines the path and direction the rotor takes through the housing.
Housing (on the picture is shown rotor inside the housing)
The housing is roughly oval in shape (it's actually an epitrochoid). The shape of the combustion chamber is designed so that the three tips of the rotor will always stay in contact with the wall of the chamber, forming three sealed volumes of gas.
Each part of the housing is dedicated to one part of the combustion process. The four sections are: Intake, Compression, Combustion and Exhaust
The intake and exhaust ports are located in the housing. There are no valves in these ports. The exhaust port connects directly to the exhaust, and the intake port connects directly to the throttle (carburator or injection system).
Output Shaft
The central drive shaft, also called an eccentric shaft or E-shaft, passes through the center of the rotor and is supported by bearings. The rotor both rotates around an offset lobe (crank) on the E-shaft and makes orbital revolutions around the central shaft. The spinning of the rotor is caused by a stationary gear fixed to the side housing that the gear in the rotor rides on. Seals at the corners of the rotor seal against the periphery of the housing, dividing it into three moving combustion chambers. Fixed gears mounted on each side of the housing engage with ring gears attached to the rotor to ensure the proper orientation as the rotor moves.
The output shaft has round lobes mounted eccentrically, meaning that they are offset from the centerline of the shaft. Each rotor fits over one of these lobes. The lobe acts sort of like the crankshaft in a piston engine. As the rotor follows its path around the housing, it pushes on the lobes. Since the lobes are mounted eccentric to the output shaft, the force that the rotor applies to the lobes creates torque in the shaft, causing it to spin.
A rotary engine is assembled in layers. Each layer is actually one oval-shaped rotor housing. Coolant flows through passageways surrounding all of the pieces. The two end layers contain the seals and bearings for the output shaft. They also seal in the two sections of housing that contain the rotors. The inside surfaces of these pieces are very smooth, which helps the seals on the rotor do their job. An intake port is located on each of these end pieces.
There are several defining characteristics that differentiate a rotary engine from a typical piston engine.
Wankel engines are considerably simpler and contain far fewer moving parts. For instance, because valving is accomplished by simple ports cut into the walls of the rotor housing, they have no valves or complex valve trains; in addition, since the rotor is geared directly to the output shaft, there is no need for connecting rods, a conventional crankshaft, crankshaft balance weights, etc. The elimination of these parts not only makes a Wankel engine much lighter (typically half that of a conventional engine of equivalent power), but it also completely eliminates the reciprocating mass of a piston engine with its internal strain and inherent vibration due to repeated acceleration and deceleration, producing not only a smoother flow of power but also the ability to produce more power by running at higher rpm.
Because of the quasi-overlap of the power strokes that cause the smoothness of the engine, and the avoidance of the 4-stroke cycle in a reciprocating engine, the wankel engine is very quick to react to throttle changes and is able to deliver a near-instantaneous surge of power when the demand arises, especially at higher rpms counts. This is more true when compared to 4 cylinder reciprocating engines and less true when compared to higher cylinder counts.
In addition to the enhanced reliability by virtue of the complete removal of this reciprocating stress on internal parts, the engine is constructed with an iron rotor within a housing made of aluminium, which has greater thermal expansion. This ensures that even a severely overheated Wankel engine cannot seize, as would likely occur in an overheated piston engine. This is a substantial safety benefit in aircraft use since no valves can burn out.
Due to a 50% longer stroke duration compared to a four stroke engine, there is more time to complete the combustion. This leads to greater suitability for direct injection. A Wankel rotary engine has stronger flows of air-fuel mixture and a longer operating cycle than a reciprocating engine, so it realizes concomitantly thorough mixing of hydrogen and air. The result is a homogeneous mixture, which is crucial for hydrogen combustion.
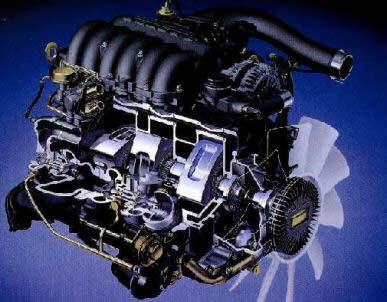
Three rotor Mazda wankel race motor
Just as the shape of the Wankel combustion chamber prevents preignition, it also leads to incomplete combustion of the air-fuel charge, with the remaining unburned hydrocarbons released into the exhaust. While manufacturers of piston-engine cars were turning to expensive catalytic converters to completely oxidize the unburned hydrocarbons, Mazda was able to avoid this cost by enriching the air/fuel mixture and increasing the amount of unburned hydrocarbons in the exhaust to actually support complete combustion in a 'thermal reactor' (an enlarged open chamber in the exhaust manifold) without the need for a catalytic converter, thereby producing a clean exhaust at the cost of some extra fuel consumption. World gasoline prices rose sharply at the time Mazda introduced their Wankel engine, making the cleaner exhaust/increased fuel consumption trade off an unwelcome one for consumers.
In Mazda's RX-8 with the Renesis engine, fuel consumption is now within normal limits while passing California State emissions requirements.
While a four-stroke piston engine makes one combustion stroke per cylinder for every two rotations of the crankshaft (that is, one half power stroke per crankshaft rotation per cylinder), each combustion chamber in the Wankel generates one combustion stroke per each driveshaft rotation, i.e. one power stroke per rotor orbital revolution and three power strokes per rotor rotation. Thus, power output of a Wankel engine is generally higher than that of a four-stroke piston engine of similar engine displacement in a similar state of tune; and higher than that of a four-stroke piston engine of similar physical dimensions and weight.
Wankel engines also generally have a much higher RPM-s than a reciprocating engine of similar power output, mostly because of the gearing from the rotor to the e-shaft; and also because the smoothness inherent in the circular motion, which eliminates dangerous vibration that can occur in reciprocating engines due to the nature of their operation.
National agencies that tax automobiles according to displacement and regulatory bodies in automobile racing variously consider the Wankel engine to be equivalent to a four-stroke engine of 1.5 to 2 times the displacement; some racing sanctioning bodies ban it altogether, including Formula 1.
Unlike a piston engine, where the cylinder is cooled by the incoming charge after being heated by combustion, Wankel rotor housings are constantly heated on one side and cooled on the other, leading to high local temperatures and unequal thermal expansion. While this places high demands on the materials used, the simplicity of the Wankel makes it easier to use alternative materials like exotic alloys and ceramics. With water cooling in a radial or axial flow direction, with the hot water from the hot bow heating the cold bow, the thermal expansion remains tolerable.
Aside from being used for internal combustion engines, the basic Wankel design has also been utilized for air compressors, and superchargers for internal combustion engines, but in these cases, although the design still offers advantages in reliability, the basic advantages of the Wankel in size and weight over the four-stroke internal combustion engine are irrelevant. In a design using a Wankel supercharger on a Wankel engine, the supercharger is twice the size of the engine.
There are few serious disadvantages. Apex seals are not perfect seals. Each has a gap in fact to allow for expansion. Moreover the sealing at the Wankel apexes is less critical, as leakage is between adjacent chambers on adjacent strokes of the cycle, rather than to the crankcase. However, the less effective sealing of the Wankel is one factor reducing its efficiency, confining its success mainly to applications such as racing engines and sports vehicles where neither efficiency nor long engine life are major considerations.
The trailing side of the rotary engine's combustion chamber develops a squeeze stream which pushes back the flame front. With the conventional two spark-plug or one spark-plug system and homogenous mixture, this squeeze stream prevents the flame from propagating to the combustion chamber's trailing side in the mid and high engine speed ranges. This is why there can be more carbon monoxide and unburnt hydrocarbons in a Wankel's exhaust stream. A side port exhaust, as is used in the Mazda Renesis, avoids this because the unburned mixture cannot escape. The Mazda 26B, famous Le Mans 24 hour endurance race winner avoided this issue through a 3-spark plug ignition system. As a result, at the Le Mans 24 hour endurance race in 1991, the 26B had significantly lower fuel consumption than the competing reciprocating piston engines. All competitors had the same amount of fuel available, because of the Le Mans 24h limited fuel quantity rule.
Mazda wankel four rotor LeMans race motor
Perhaps the most exotic use of the Wankel design is in the seat belt pre-tensioner system of some Mercedes-Benz cars. In these cars, when deceleration sensors sense a potential crash, small explosive cartridges are triggered electrically and the resulting pressurized gas feeds into tiny Wankel engines which rotate to take up the slack in the seat belt systems, anchoring the driver and passengers firmly in the seat before any collision