Nose Cone
Follow this link to check my article about new 2014 nose cone rule and designs.
![]() |
![]() |
![]() |
Long time ago, when aerodynamics where not so important, driver safety was small man talk and not in use in F1, nose cone (front of the car in those times), was not important piece of car structure. Constructors main aim was to make car look aggressive and cool, and to house engine and radiators. Nothing more and nothing less.
While the nose cone or nose box today is mainly designed for aerodynamic efficiency it must also comply with several strength and measurement rules that are set by the FIA. Not only must it absorb energy in the case of a head-on collision, it must also support the front wing.
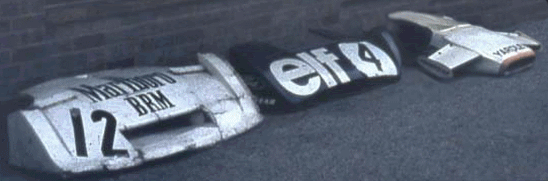
Nose cone of BRM P160 (1973), Tyrrell 006 (1973) and McLaren M19 (1973) side by side
Let see first about driver safety
Let's be known that all this apply to rear crush structure too. Rear impact structure is structure hanging behind gearbox and often support rear wing.
In a Formula One crash we can often see thousands of carbon fiber shreds flying in all directions and you would think that the crash was huge and very dangerous. An F1 nose cone or rear crush structure falls apart pretty easily (comparing to monocoque) in a knock. It's only the drivers safety cell and a selected few other bits that are still any good after crash.
That's the whole idea. In the event of an accident the nose cone and rear crush structure are what is known as a sacrificial crash structures.
Every component fitted to the safety cell, e.g. nose cone, side pods, rear wing, suspension, rear crush structure etc is designed to deform and disintegrate in controlled way in the event of an impact.
Its all about reducing the impact energy and the negative acceleration (or deceleration) acting upon the driver.
Tire walls perform the same job - they usually consist of a rigid steel barrier or wall, covered in deformable tires or barrels filled with water.
All in all the tire wall will deform by about a meter, whilst the car crush structure may deform by about half a meter (more or less length of nose cone), for example.
Made of carbon fiber impregnated with resin outer skin with honeycomb cores and thinner inner layer of carbon fibre, the nose brake inwards to absorb a frontal crash. The structure is laminated in such way to provide the most effective energy-absorbing properties. During its construction, individual layers of carbon fiber are layered in the way that the nose cone deformation and car's deceleration is controlled progressively. The beauty of composite construction is that you can put plies exactly where they need to be to optimize the load-bearing requirement.
Properties of carbon fiber components are very reliant on the characteristics of the original materials (preimpregnated, weave type, unidirectional, low density, high density etc) and the manufacturing process.
In other words, its all very well saying that carbon fiber is X times stronger than steel, and X times lighter. In general terms this is true - it can be made that strong and light. But it doesn't mean that these guys are actually making it that strong.
In an accident the function of the carbon fiber is to absorb as much of the impact energy as is physically possible. Carbon fiber does this by first deforming, then secondly shattering in well calculated way, rather than sending shock waves through the entire monocoque structure to the driver. This is why we see in an accident all the shards of Carbon fiber flying everywhere.
Each new nose box design must pass two mandatory crash tests, one a static side load test and the other an impact test. In these tests, the nose box is fitted to a monocoque - complete with driver dummy and gas tank full of water - mounted on a trolley and crashed into a wall. To pass the test, all the energy must be absorbed by the nose box, with no damage incurred to the monocoque or dummy. People often comment that the test speed of 15 meters per second (54 km/h) is not very fast compared with the speed at which a Formula 1 car travels, but during the test the car is in effect hitting an immovable brick wall, and on the circuit the crash barriers take big part of the energy so not all of it is absorbed by the nose box itself. Upon impact, the carbon fiber will turn to dust.
For more info about crash test go to "Crash test" page.
There was another safety issue for driver, marshals and public. Since F1 cars have a minimum weight set by the FIA and all teams have a lighter car they can move ballast around the car to where it can be used best for performance. The tip of the nose is an interesting place since it is actually in front of the front wheels while the distance between the front wheel axis and the ballast acts as a lever. The extra weight in the noses became a serious danger in 2005. Suppose an accident happens and part of a nose cone gets thrown up onto another car or public. The more the weight, the more damage it may cause there. From 2006 on the FIA decided to impose a ban on ballast weight inside nose cone. Anyway, teams still use front wings or front wing endplates to position some additional ballast in specially made slots.
And now about aero characteristics
A group of rules in both the bodywork and chassis rules dictate the geometry for the nose cone. On the end, the nose is an aerodynamic feature, but largely influenced by the need to pass a range of crash tests and need to act as a mounting point of the front wing to the chassis. FIA is controlling overall position, height and the size of the bulkheads in the front of the driver feet. This area is defined by dimensions of the front bulkhead (FIA section A-A). Next dimension is bulkhead distance from the cockpit opening.
Height and cross section in this area is critical as teams want a minimal cross section in between the front wheels and as much space as possible underneath to fit bodywork to direct airflow around and under the sidepods. So teams will tend to raise these bulkheads as high as they can go. Teams tend to have an angled upper surface to the nose cone and a “V” cross section to the front bulkhead, to make the surfaces more aerodynamically efficient. The nose tip must meet a minimum and maximum tip height, this means that the area 50mm behind the actual tip must be centred at predefined high above the cars reference plane (the bottom of the stepped floor). The cross section for the tip must be 9000mm2 or more which equates to a 97mm square or 107mm diameter circle, but the actual shape is relatively free within these parameters. In terms of length the nose can not be shorter than front wing centre section and can extend forwards beyond the front wing.
At first sight the higher nose is equal to less downforce as by itself it pushes less air up over the nose. One area of the car in particular attracted constructor's attention: the underbody airflow. While true ground effect designs had been banned during the 1980s, the contemporary practice of coupling a flat, stepped chassis undertray with a large rear diffuser meant that many cars still produced a significant proportion of their downforce through the generation of a low-pressure air mass underneath the car.
What Postlethwaite (in this time Tirrell Racing Team lead designer) and his team realized was that the efficiency of this low-pressure generating system was being seriously compromised by the low nose position at the front end of the car. These low nose cones effectively diverted air sideways and upwards around the cars' upper bodywork, and reduced the volume of air passing underneath the car. However, the generation of low pressures relies on increasing the speed of the air passing underneath the car, in relation to air passing over and around it. Having high nose allows air to go straight through under the nose instead of having to go around it. While it reduces drag, all air that passed under the nose is then guided under the car or split to either side of the car by the splitter located just in front of the sidepods.
In simple terms, the more air that can be drawn underneath a car, the faster that air will have to be moving, and the faster the air is moving, the lower the pressure (remember Bernouly?).
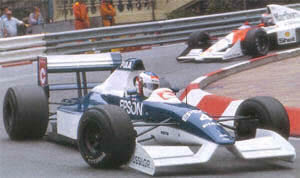
Tyrrell 019
By rising the nose cone of the car, Postlethwaite and his team increased the volume of air that was able to pass underneath the car. Conversely, the efficiency of the front wing aerofoil is increased the closer they are to the ground. These conflicting requirements led to the design of the Tyrrell 019's distinctive inverted V, anhedral front wing profile. He left center part below the nose tip without any aerofoil to further free the way for fresh non disturbed air to feed undertray and diffuser.
With improvement in aero research, constructors further improve design. Before regulation changes 2008, front wing was fitted complete width of the car, and part below nose tip further increasing downforce of the front wing. They where using different wing profiles in this area. Most used profile was so called "spoon" profile.
Today central part of the wing below the nose is same profile for all cars, must be flat and can not produce any downforce.
With the regulations around what designers can do at the rear of the car now more tightly controlled than ever, the front of the car naturally comes in for increased attention and is where constructors are been focusing on – trying to improve airflow going over the car. Classically of course, you are looking for lower drag and higher downforce. In the case of nose cone and front wing, there’s the attachment pylons – which you may have noticed are quite a lot different from car to car – and then the wing’s flap and end plates. With atention on front of the car, eg. nose cone and front wing, you’re managing the airflow that is enjoyed by the rest of the car, downforce generating surfaces and other features of the car. You can often generate more performance by managing the flow that arrives at rest of the car than developing them themselves. It’s nowadays quite a critical part of the car – you’re looking to find very small improvements.
Sometime after the accidents and damaged nose cone or front wing, mechanics have to change whole assembly very quickly. It is the question of seconds, race position, points, and on the end championship. During the years teams used different ways to fix nose to the monocogue, and most obvious way was to use bolts. Bolting the nose in place was a very secure method of retention, in an emergency pit-stop following a front wing shunt, the mechanics would take far too long trying to replace the damaged nose. Teams use to have a couple of small air-guns in the pit-lane, set and reserved just in case of a possible nose change.
John Barnard was a perfectionist, his attention to detail is legendary, and there were some fine details to the design of the Beneton 1991 F1 car B191. It is usual that the radiator side-pods covers of a Grand Prix car are secured to the chassis with a number of individual bolt fixings around the edges of the pod. However, as the side-pods are removed two or three times each day of a race weekend this becomes a tedious and time-consuming matter – plus one always runs the risk of ‘rounding’ an over-tight bolt in the process of trying to remove it. In an ingenious way of improving this situation, Barnard’s team had developed a flush-fitting quick-release catch. Operated by a special two-pronged key, this simple though brilliant design feature enabled both side-pods to be removed from the chassis in a matter of seconds.
2013 Toro Rosso parts of the quarter turn fastening system that hold the nose onto the chassis (picture of Toro Rosso's youtube video of a factory tour)
One feature of John’s Beneton car which has been copied on to every Formula One car in the pit-lane is his quick-release catch for the nose and front wing assembly. This was another brilliant piece of ingenuity, and one which should have won his team a trophy for Formula One design excellence. The idea wasn’t new, since it was based on the plastic snail-cam fasteners found in quick-build kitchen units in the big DIY warehouses. Push a dowelled peg into the body of the snail-cam and an Allen key turns the cam through 180 degrees, locking the two parts together. Job finished. Brilliant! Other teams were still using bolts, though most soon relented once they noticed a possible alternative, but Williams Grand Prix Engineering continued to use this method as the last to change, but couldn’t hold back the tide any longer and they too fitted a version of the Barnard nose catch.
But let's see how all this high nose thing started
The Tyrrell 019 was a first F1 car having an elevated nose cone. This was the first time that such an idea had been tried in Formula One racing, and it set the way F1 cars have been designed until today. The car was introduced two races into the 1990 Formula One season, scoring a point on its debut in the hands of Jean Alesi. This type of nose cone was gradually adopted by other teams. The car was powered by a 3.5L Cosworth DFR V8 - a descendant of the legendary Cosworth DFV.
The Tyrrell 019 was designed by Harvey Postlethwaite, and built by Tyrrell racing team. It was an evolution of Postlethwaite's first design for Tyrrell, the Tyrrell 018. Taking the 018 as his base, Postlethwaite decided to try and improve the aerodynamic efficiency of the chassis. Postlethwaite was an experienced F1 engineer, having previously built race-winning cars for Hesketh, Wolf and Ferrari, and so was well-placed to spot the shortcomings of his own design. It was however an early idea and primitive type of high nose as several important points of a high nose design were not understood well. As the years have evolved, the mechanical parts have become smaller and smaller increasing the advantages of a small high front nose. In 1996 all low nosed cars had disappeared in favor of the higher alternative.
In practice the car did not make the same impact in terms of results as it has in technological advancement. Although Alesi qualified a strong seventh and took a point for a sixth place finish at its first race in San Marino, and then both qualified and finished in second place in Monaco, the remainder of the season resulted in only two points finishes. Nevertheless, as other teams experimented with the principle it rapidly became the norm for Formula One cars to sport a high nose cone. After this car, all Formula One Championship winning chassis have followed Tyrrell's lead.
The Tyrrell 019 was replaced at the end of the 1990 season by the Tyrrell 020, a further evolution of Postlethwaite's high nose principle.
The last really good performing low nose car was Williams FW15 built only four years after the Tyrrell's unveiling their Tyrrel 019. While Prost won the 1993 championship in his comeback year, the next year Williams FW16 driven by Airton Sena 1994 was still very good
but outraced by Benetton's
Michael Schumacher who took his first championship. Prost has his enter in the history books as the last man to win the championship with a low nosed car.
Williams and its chief designer Adrian Newey implemented a high nose with their 1995 challenger, the Williams FW17 was a runner up in the hands of Damon Hill and a championship winner the next two years.
FIA 2012 season Technical and Sporting Regulations changes prescribe that the car noses are lowered to 550mm above the reference plane (previously they could be 625mm high). This is to ensure that all parts of the nose are definitely below the height of the cockpit sides in the event of a T-Bone type of crash.
Few different nose cone designs
Design of 2010 nose cones
![]() |
![]() |
Force India nose cone, 2010 |
Renault nose cone, 2010 |
![]() |
![]() |
Red Bull RB6 Nose cone 2010 |
Lotus nose cone, 2010 |
![]() |
![]() |
Hispania Racing Team nose cone, 2010 |
Ferrari 2010 nose cone |
A1GP car frontal crash test
Follow this link to check my article about new 2014 nose cone rule and designs.