Carbon Fiber
![]() |
![]() |
Carbon fiber (alternately called graphite fiber) is a polymer (made from another polymer, called polyacrylonitrile, by a complicated heating process) which is a form of graphite material consisting of extremely thin fibers about 0.005-0.010 mm in diameter and composed mostly of carbon atoms. The carbon atoms are bonded together in microscopic crystals (hexagonal aromatic rings) that are more or less aligned parallel to the long axis of the fiber. The crystal alignment makes the fiber incredibly strong for its size. Several thousand carbon fibers are twisted together to form a yarn, which may be used by itself or woven into a fabric. Carbon fiber can be combined with epoxy and wound or molded to form composite materials such as carbon fiber reinforced plastic (also referenced as carbon fiber) to provide a high strength to weight ratio material. The density of carbon fiber is also considerably lower than the density of steel making it ideal for applications requiring low weight. The properties of carbon fiber such as high tensile strength, low weight, and low thermal expansion make it very popular in aerospace, military, and motorsports along with other competition sports. The unique appearance of carbon fiber also makes it popular for stylistic purposes.
These fibers are not used by themselves. Instead, they're used to reinforce materials like epoxy resins and other thermosetting materials. We call these reinforced materials composites because they have more than one component.
Carbon fiber Specific elastic Modulus |
Carbon Fatigue resistance |
![]() |
![]() |
Carbon fiber reinforced composites are very strong for their weight. They're often stronger than steel, but a whole lot lighter. Because of this, they can be used to replace metals in many uses, from parts for airplanes and the space shuttle to tennis rackets and golf clubs.
Carbon fiber, stronger than steel, and much lighter. How they make it?
They start off with another polymer, called polyacrylonitrile. They take this polymer, and heat it up. They are not sure just exactly what happens when they do this, but we do know that the end result is carbon fiber. They think the reaction happens something like this: when they heat the polyacrylonitrile, the heat causes the cyano repeat units to form cycles!
Then they heat it again! This time they turn the heat up higher, and our carbon atoms kick off their hydrogens, and the rings become aromatic. This polymer is a series of fused pyridine rings.
Then they heat it...AGAIN! Slow roasting the polymer something more, at around 400-600°C causes adjacent chains to join together.
This expels hydrogen gas, and gives us a ribbon-like fused ring polymer.
But they are not done yet! Next they crank up the heat, anywhere from 600 all the way up to 1300ºC. When this happens, our newly formed ribbons will join together to form even wider ribbons.
When this happens, they expel nitrogen gas. On the polymer we get, it has nitrogen atoms along its edges, and these new wide ribbons can then merge to form even wider ribbons.
As this happens, more and more nitrogen is expelled. When we're through, the ribbons are really wide, and most of the nitrogen is gone, leaving us with ribbons that are almost pure carbon in the graphite form. That's why we call these things carbon fibers.
Spools of row Carbon fiber
|
![]() |
Plain Weave |
![]() |
2X2 Twill Weave |
![]() |
4X4 Twill Weave |
![]() |
5 Harness Satin |
![]() |
8 Harness Satin |
Carbon fibers, under industrial production now, are classified into PAN-based, pitch-based and rayon-based. Among them, PAN-based carbon fiber is in the largest production and best used in volume. In the beginning of 1970's, commercial production of PAN-based and isotropic pitch-based carbon fibers was started on a large scale. In the latter half of 1980's, anisotropic pitch-based carbon fiber manufacturers broke into the market.
Usage of carbon fiber by itself is not the rule. Commonly, customers apply carbon fibers for reinforcement and / or functionality of composite materials, made with resin, ceramic or metal as matrix. Carbon fibers are extensively applied to a large variety of applications with supreme mechanical characteristics (specific tensile strength, specific modulus) and other characteristics due to carbon matter (low density, low coefficient of thermal expansion, heat resistance, chemical stability, self-lubricity, etc.).
Carbon Fibers, having supreme characteristics, are adopted in wide varieties of uses. Suppliers are able to provide, by using different raw material and applying divergent production processes, wide diversity of the fibers having different specifications.
PAN Type Carbon Fiber A type of the fiber, produced by carbonization of PAN precursor (PAN: Polyacrylonitrile), having high tensile strength and high elastic modulus, extensively applied for structural material composites in aerospace and industrial field and sporting / recreational goods.
PAN Type Carbon Fiber is an aggregation of continuous fiber (filaments), 5 – 7 micron meter in diameter with 1.74 - 1.95 g/cm3 of density, generally. Products with various filaments, such as 1K (1000 filaments), 3K (3000 filaments), 6K (6000 filaments), 12K (12000 filaments) and 24K (24000 filaments), referred to as "Regular Tow" or "Small Tow", have been used in large quantity for aircrafts and sports/recreational fields, making good use of low density, high specific tensile strength and high specific elastic modulus. PAN fibers have been undertaken a role for market expansion of carbon fibers.
Large Tow, extra-40K, even though slightly lower tensile strength is mainly used for industrial fields as a relatively inexpensive material, along with Regular Tow. PAN type carbon fibers are classified into Standard Elastic Modulus Type (- 240 GPa), Intermediate Elastic Modulus Type (- 300 GPa) and High Elastic Modulus Type (350 GPa -).
Pitch Type Carbon Fiber Another type of the fiber, produced by carbonization of oil/coal pitch precursor, having extensive properties from low elastic modulus to ultra high elastic modulus. Fibers with ultra high elastic modulus are extensively adopted in high stiffness components and various uses as utilizing high thermal conductivity and / or electric conductivity.
Regarding Pitch Type Carbon Fiber, there are continuous type and discontinuous type, based on respective spinning process.
Pitch Type Carbon Fiber is also classified into Isotropic Type (hardly-graphitizability) and Un-isotropic Type (easy-graphitizability), based on respective raw pitch. Isotropic Pitch Type Carbon Fiber is commonly a discontinuous fiber of 12 - 18 micron meter in diameter with 1.6 g/cm3 of density and has the properties of low modulus (- 40 GPa), strength and thermal conductivity due to its weak structural orientation of carbon atoms and underdeveloped graphite crystallinity. With its competitive cost, Isotropic Pitch Type Carbon Fiber is extensively applied for industrial fields due to light weight, chemical stability, heat resistance and abrasion characteristic.
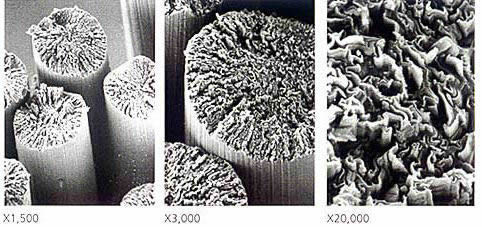
Carbon fiber under microscope
On the other hand, Un-isotropic Pitch Type Carbon Fiber is sometimes referred to as "Mesophase Pitch Type Carbon Fiber". This fiber is commonly a continuous fiber (filaments) of 7 - 10 micron meter in diameter with 1.7 - 2.2 g/cm3 of density. There are 1K, 2K, 3K, 6K and 12K as filaments per tow and wide variety of elastic modulus grades from 6 GPa (the lowest) to 953 GPa (the highest), whereas PAN Type Carbon Fiber cannot achieve this range. High Elastic Modulus Type Carbon Fiber (350 GPa -) has excellent process ability due to high tensile strength, more than 2.5 GPa, and has been extensively applied for industrial and sports/recreation fields utilizing higher stiffness than iron and light weight (50% or less than iron) as molded composite materials. Applications for Ultra High Elastic Modulus Type Carbon Fiber (600 GPa -) are expanding, utilizing excellent stiffness, equivalent or higher thermal conductivity to metals and lightness in weight.
Plain weave fabric surface finish smoothness |
Spread tow fabric (STF) deliver improved surface smoothness by reducing interlacing points |
As technology advancing from year to year, in the last few of them new fibres and resin systems offering improved mechanical and thermal capabilities, entered in Formula 1, coveted by Formula One engineers. This advancement is visible especialy in area of design of the weave for composite fabrics.
Most Formula One components are traditionally manually laminated using continuous pre-impregnated (pre-preg) carbon fibre reinforcements with either unidirectional (UD) fibres or woven fabrics, as explained before, often referred to as cloth.
![]() |
Ferrari F14T 2014 showing interrior of his sidepods woven with STF |
Conventional cloth weave designs commonly include plain weaves, 2 x 2 twills and satin weaves. Each of these have different surface finish smoothness and strenght. The combination of different characteristics in each individual weave style have some level of compromise, and this has driven the research and optimisation of weave design. Advances in textile engineering and manufacturing have resulted in the development of spread tow fabric (STF) materials. Instead of ‘bundling’ the carbon fibres in narrow and thick tows, spreading the fibres into thin and wide tapes and then weaving these together allows ultra-lightweight fabrics to be produced. This offers a number of benefits over the more traditional cloth designs. The flat structure of STFs reduces the frequency of crimp angle (the undesirable distortion of the fibres produced by the interlacing of the warp and weft tows detrimental to mechanical performance) while improving the resin wet-out (resin impregnation of the fibre reinforcements). This results in high fibre volume with straighter fibres, increasing the mechanical properties of the laminate while reducing the amount of excess resin, therefore minimizing weight from of 20 to 30%, giving mechanical performance similar to a cross-ply construction made using UD (unidirectional) tapes. STF also deliver improved surface smoothness by reducing interlacing points.
![]() |
Engine cover woven with combination of STF and unidirectional (UD) fibres or woven fabrics often referred to as cloth, as required. |
Ultimately the significant weight savings, improved mechanical properties and thinner laminates are why STFs have found a home in Formula One racing cars, with many components – including the monocoque, bodywork and floors – benefiting from the superior performance this composite offers.
"Light in weight, Strong and Durable!" Carbon Fibers are nothing but a 21st. century high technology material. The fibers have low specific gravity, exquisite mechanical properties (high specific tensile strength, high specific elastic modulus, etc.) and attractive performances (electric conductivity, heat resistance, low thermal expansion coefficient, chemical stability, self-lubrication property, high heat conductivity, etc.). Those features have been stimulating Carbon Fiber users to develop numerous kinds of applications.
Dr. Roger Bacon created the first high performance carbon fibers at the Parma Technical Center outside of Cleveland, OH. The first fibers were manufactured by heating strands of rayon until they carbonized. This process proved to be inefficient, as the resulting fibers contained only about 20% carbon and had low strength and stiffness properties. In the early 1960s, a process was developed using polyacrylonitrile as a raw material. This produced a carbon fiber that contained about 55% carbon and had much better properties. The polyacrylonitrile conversion process quickly became the primary method for producing carbon fibers.
On the 14th January 1969, Carr Reinforcements wove the first ever Carbon fibre fabric in the world.
During the 1970s, experimental work to find alternative raw materials led to the introduction of carbon fibers made from a petroleum pitch derived from oil processing. These fibers contained about 85% carbon and had excellent flexural strength.
Manufacturers:
PAN aerospace/high end carbon fibre:
Toray (largest worldwide manufacturer)
TohoTenax
Mitsubishi
Hexcel
Cytec
Nippon Graphite Fiber Corporation