CFD
Computational Fluid Dynamics
Since the introduction of the super computers in the 1980's, the use of Computational Fluid Dynamics (CFD) for solving fluid flow problems has increased dramatically as a numerical tool in many areas of engineering.
The pictures overview below from some of CFD projects through the years has focused on space transportation systems, aeronautics, sport aerodynamics, building aerodynamics and surface transportation. Hence, the marine aspect of CFD analysis, has many commonalities with the topics illustrated below.
The development of Wind Tunnel technology that Formula 1 ofer to the world, important though it has been, pales into insignificance alongside the rapid growth of Computational Fluid Dynamics (CFD). With a wind tunnel, experiments are made by blowing wind over a real object in a controlled environment and measuring the aerodynamic forces that arise. In CFD, the same experiment may be conducted in the form of a computer simulation. Although the equations that govern these computations have been understood since the 1930s, they are very complex to solve and require the sort of computing power that has only become availible in the last 10 to 15 years. A huge range of industries benefit from the mastery of aerodynamic design that a successful CFD programme enables. It is probably no surprise that the aerospace, road car and wind turbine industries use CFD in their design process. It might be less obvious that it also brings significant advantage in hundreds of other industries. In fact, in any application where there is any sort of fluid (gas or liquid) flow, CFD can bring benefit. Climate modelling, the force of wind on a building, the way in which medicine is distributed in an inhaler, efficient air conditioning design, transport of gas or liquids in pipelines; the list of applications is truly enormous. All of these applications benefit, to a greater or lesser extent from the investment that Formula 1 has made in the growing technology of CFD. For a sustained period of around 20 years, the teams in Formula 1 have invested money into the development of CFD systems and programs, as it has been clear for a long time that this tool would be a usefull prerequisite for success in the sport. Teams have sponsored the development of improved CFD techniques at top universities and they have also put money directly with the providers of commercial CFD software to ensure that the considerable challenge of accurately simulating the aerodynamic behaviour of a Formula 1 car has turned from an aspiration to a reality. It would be wrong to pretend that the development of subsonic CFD codes has been the sole responsibility of the Formula 1 industry, but no serious observer of the industry would deny that the combined investment of the teams has been very significant.
In racing car industry, Computational Fluid Dynamics (CFD) is an emerging science in the aerodynamic design area; during the last decade aerodynamicists found a growing interest in using computers and CFD methods to simulate wind tunnel tests or track conditions. Briefly CFD codes simulate the flow over a car through mathematical modelling and solving of a discrete model.
![]() |
![]() |
There are three compelling reasons why F1 teams and industry start to use CFD software:
insight, foresight, and efficiency.
Insight
If you have a device or system design which is difficult or expensive to prototype or test through experimentation, CFD analysis enables you to virtually crawl inside your design and see how it performs. There are many phenomena that you can witness through CFD, which wouldn't be visible through any other means. CFD gives you a deeper insight into your designs.
Foresight
Because CFD is a tool for predicting what will happen under a given set of circumstances, it can quickly answer many 'what if?' questions. You provide a set of boundary conditions, and the software gives you outcomes. In a short time, you can predict how your design will perform, and test many variations until you arrive at an optimal result. All of this can be done before physical prototyping and testing.
Efficiency
The foresight you gain from CFD helps you to design better and faster, save money, meet regulations and ensure FIA rules compliance. CFD analysis leads to shorter design cycles and teams can get their car to track faster. In addition, equipment improvements are built and installed with minimal downtime. CFD is a tool for compressing the design and development cycle allowing for rapid prototyping.
![]() |
2010 Yamaha YZR M1 MotoGP engine air box air flow, speed and pressure |
Nowadays CFD and FEA are a necessary basic tools for the design and development of racing cars, helping wind tunnel research. In fact it's possible to test the car prior to any wind tunnel session, so as to pre-evaluate various configurations and submit to test only the most promising solutions.
CFD substantially helps with understanding the phenomena involved in fluid flows, permitting accurate display and analysis of the information, with a level of detail that is hard to provide experimentally.
Some other examples of use of CFD:
![]() |
![]() |
Air flow of air entering cylinders of racing car |
Air flow around front F1 wheel |
From BMWSauber site about "Albert":
Computational fluid dynamics (CFD) offers apparently limitless options
when it comes to the calculation process in the development of aerodynamics components. However, it does require extremely large computer-based capacity. To this end, the BMW Sauber F1 Team can count on one of the most powerful supercomputers not only in Formula One, but in the automotive industry as a whole. "Albert", as the system has been christened, was built using a total of 530 64-bit processors by Swiss firm DALCO. The software is supplied by Fluent.
CFD helps to calculate the design of aerodynamic components and is an important complement to wind tunnel work. "Aerodynamics has been gaining steadily in importance over recent years. And this means that computational fluid dynamics has also become increasingly important", explains Willy Rampf, ex technical director.
Altogether, the new Sauber supercomputer comprises 530 processors in a cluster architecture with dual nodes. The processors are installed in high-density cooling enclosures supplied by American Power Conversion (APC). These enclosures are self-contained, closed-loop water circuits that provide up to 15 kW of cooling power per enclosure. The supercomputer comprises a total of ten enclosures, each one metre wide, a 1.20 metres deep and 2.30 metres high, resulting in a total width of ten metres and a weight of
18 tonnes.
The technical data is as impressive as the "hard facts": the supercomputer boasts peak performance of 2.3 Tflop/s and is equipped with 1 TB RAM and 11 TB of hard-drive storage
To illustrate the point for non-computer experts, this means that "Albert" is capable of performing 2,332,000,000,000 computing operations per second. To achieve the same computing performance, the entire population of the city of Zurich (350,000) would have to multiply two eight-digit figures every four seconds for a whole year. The machine has over 1,085,440 megabytes of physical memory and over 10,880 gigabytes of hard-drive storage. BMW Sauber use all this power for calculations in CFD and FEA.
The virtually unlimited technical possibilities of the Sauber supercomputer are used for analysis in the field of aerodynamics. CFD and FEA are used in the computer-aided calculation of aerodynamic components for the Formula One race car. This involves the use of numerical grid models that are made up of a maximum of 100 million cells. Thanks to the new supercomputer, it will be possible to further refine these models, thus improving the quality of the results significantly. The extremely short calculation times possible with "Albert" allow a large number of different variants to be evaluated. In addition, complex driving situations can be simulated. CFD plays an important role in the development of front, rear and auxiliary wings as well as in engine and brake cooling.
![]() |
Unsteady CFD simulation and shape optimisation techniques were used to make gains for wheelchair and track cycling in 2012 (Courtesy of UKSport and TotalSim) |
Computational fluid dynamics is intended to complement, rather than replace, the work in the wind tunnel. Indeed, CFD and experimental work in the wind tunnel are closely interlinked and thus generate valuable synergies benefiting both sides.
In the development of a new front wing, up to 100 variants are evaluated in two-dimensional form before roughly half a dozen of them are analyzed in 3D. The most promising versions are subsequently built for the 60-percent model and tested in wind tunnel. CFD thus enables the wind tunnel to be used particularly efficiently.
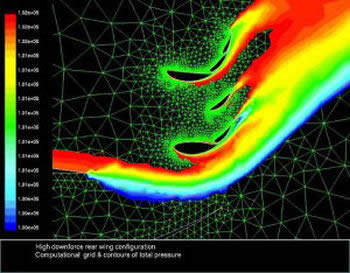
CFD of full rear wing configuration pre 2008
I have to say something about modern F1 cars. I doubt that there is any among all of them at the grid that has a complete correlation. A modern F1 car has so many difficult interactions between vortices, streams, wakes etc. This area is extremely sensitive, and you only need a vortex stream to move by a few centimeters and it can really change the characteristics of the car quite a lot.
There is only few good enough CFD software that can satisfy demanding Formula 1 world. Currently, most of the teams use CFdesign, Flow Science, Fluent, ANSys, Metacomp Technologies, CD-adapco and FieldView from Intelligent Light.
Aerodynamic resource restrictions in Formula One were introduced by FOTA in 2009 as a means to limit a team’s expenditure on aerodynamics. This limitations were optional and open to abuse. Large investments were being made in full-scale wind tunnels, enormous computational clusters and on-track testing, and cost start to get out of control. To prevent that, limits were placed on a team’s running full-size cars in a wind tunnel, track testing, wind tunnel usage time and CFD usage. Limitation are introduced for length of time the wind tunnel is switched on (with the speed above a nominal value) and harvested CFD teraflops (this is a measure of the computational usage of a CFD cluster).
For 2014, the testing restrictions are now an appendix to the sporting regulations, and are enforceable by the FIA. They are no longer optional and open to abuse. Beyond this, the two main changes for 2014 are:
- A reduction in the wind tunnel and CFD usage is limited to 30 hours and 30 teraflops
- The number of wind tunnel runs is limited to 80, and occupancy time is restricted to 60 hours (the length of time a model can be installed in the wind tunnel, having parts changed or ready to be tested)
Before, s Formula 1 wind tunnel will typically run for 24 hours a day, seven days a week, during which it can perform upwards of 200 runs, so the new restriction cuts this down to roughly a third of the old run rate. Assuming that each wind tunnel run is testing a new part, this is a dramatic reduction in the number of components that can be tested in the tunnel.
The reduction in wind tunnel testing will lead to a greater emphasis on the use of CFD in the development process. Designing parts in CFD prior to tunnel testing allows all but the most promising directions to be filtered out without wasting tunnel runs and time.
In year 2010, 3 new teams are invited in Formula 1 family, and Virgin Racing F1 team technical boss Nick Wirth is aiming to showcase the CFD technology outside of Formula 1 by building a successful grand prix car with it.
Wirth is designing Virgin's maiden F1 car (VR-01) using only CFD instead of the traditional wind tunnel and CFD method used by all Formula 1 teams.
He had already used this method in Acura's the American Le Mans Series car.
The miracle of the Acura ALMS programme has been the technology behind it - the simulator and the CFD.
Wirth also highlighted the importance of CFD when reducing the costs of running a Formula 1 team.
"It's absolutely critical," he added. "We did it because it's cheaper and faster. The point is that you can get more accurate aerodynamic answers for a given amount of money using this technology than any other thing.
"You can try more endplates, more rear wings and other things then the same money gets you in wind tunnel testing or full-scale testing."
He added: "We've done it before - my company built already race and championship winning cars, so we're very happy. We've also been doing open-wheel work in Formula 3 and IndyCar racing at the same time as the Acuras. We'll be using the same technology, so this isn't new to us.
He acknowledged that the CFD approach had limitations - but insisted wind tunnel testing was no different.
"We fully expect to encounter issues along the way; CFD is an approximation - as is scale-model testing," Wirth said. "In both cases, it is only when you hit the track that you can really appreciate the effect of factors that are tricky to model with any technology such as the effect that the real stiffness of all bodywork components and joints has on the airflow for example.
"Can things go wrong? Absolutely, that's life."
"If you remember last year (2009) BrawnGP brought out the new front wing development for Jenson Button to run at Suzuka, and it was a disaster, it didn't work and it screwed his race up. They have a load of aerodynamic technology which says that front wing was good, they put it on the guy trying to win the world championship at a critical race, and it didn't work."
"What must they be thinking about what they understand about aerodynamics? Everybody has problems and issues."
Update for Virgin CFD F1 project after 2 years:
In the middle of season 2011 and after two disappointing seasons in Formula One, Virgin have split with technical director Nick Wirth.
With Wirth Research behind their F1 cars, Virgin entered Formula One with a car designed solely on CFD technology. However, the car proved to be unsuccessful in first and now in second season, finishing on the bottom of the Constructors' Championship list in year one.
And although the team had expected better this season, Virgin have again failed to deliver as the car is not up to task. As such, the team has parted ways with Wirth. The dismal start to this year's Championship has forced the team to focus on next year's car with former Renault engineering director Pat Symonds, who was called up to act as a consultant, believed to be behind the team's new strategy.
Symonds is also reported supervising Virgin's 2012 car although Webb insists they are still working on improving this year's MVR02. For next year car, team want to use all testing technologies on their disposal. CFD and Wind tunnel will be in use.
Here you can see cool CFD video of F1 car CFD analysis demo by Advantage CFD (company now out of business). Video is showing BAR Honda F1 car (now out of business too) and must be from around year 2000 - 2003.
CFD Parachute simulation
PETSc-FEM CFD simulation of flow around spinning projectile
EnSight Rally Car Analysis
Water pump design Automotive CFD
Piston motion
Formula One Split Wing CDG Aerodynamics
Supercomputing in F1 - Unlocking the Power of CFD (PDF) (Larsson T and Sato T. and Ullbrand B, Sauber Petronas, 2005)